Hebei Shida Seal Group has its own internal quality inspection center, which includes one chemical analysis laboratory and one physical laboratory which are equipped with the full set of equipment and instruments for chemical analysis of raw material, mixed rubber compounds before and after curing and physical properties testing of finished products.
We test all materials and products to industrial, national standards and customer-specific requirements in-house or with third-parties. For example, we can test these properties of rubber extrusions/seals: hardness, density, tensile strength, elongation, brittleness temperature, heat aging, compression set, ozone resistance, staining in contact with organic material, corrosivity, low-temperature flexibility, low-temperature flexibility of coating, splice strength between solid &sponge, splice strength between extrusion and corner, dimensions, compression load, abrasion resistance of flock, insertion force, extraction force.
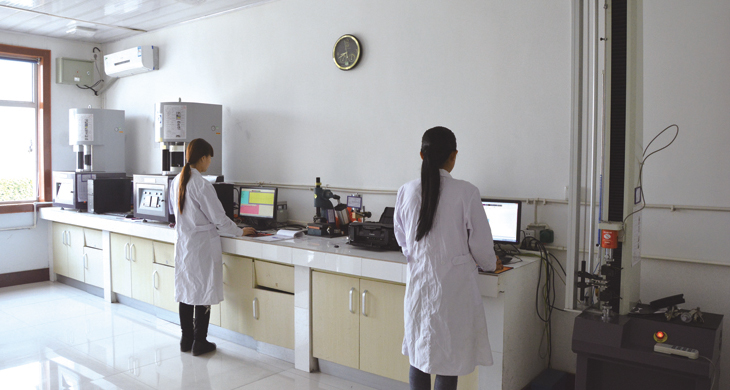
-Physical Testing
Our physical testing laboratory conducts physical / mechanical analysis of rubber and polymeric materials and testing of finished goods such as automotive sealing products, industrial rubber seals, rubber extrusions, profiles, and molded rubber parts, etc. This testing laboratory offers a full range of physical / mechanical testing services to evaluate rubber materials or components like hardness, tensile strength, compression set, tension set, elongation at break, adhesion, abrasion, aging in hot air and performance tests.
Typical Rubber Testing Equipment:
Number | Equipment Name | Usage |
#1 | Moving Die Rheometer | Measure rubber compound cure properties under isothermal test conditions with constant strain and
frequency; Measure the change in stiffness of a rubber sample |
#2 | Mooney Viscometer | Measure the change in a rubber and plastic elastomer properties over time, from uncured to scorched state. |
#3 | Tensile Strength Tester | Determination of tensile strength / elongation at break
A die cut sample of slabs molded from vulcanized rubber or TPV elastomer are mounted on either end of its length by secure clamps. The test piece is then stretched at a specific rate until elongated to break. The maximum stress at break (tensile strength) and the percentage of strain (elongation) are recorded. |
#4 | Aging Oven | Evaluate resistance to property deterioration as a result of thermal exposure.A variety of physical properties (tensile strength, elongation,hardness, etc.) as well as aesthetic qualities (color, gloss, etc.) after prolonged heat exposure are evaluated and rated compared to pre-exposure attributes. |
#5 | Flock / Coating Abrasion
Resistance Tester |
Measure the abrasion resistance of flocked surfaces.To validate the durability of low friction surfaces through repeated abrasive conditions. |
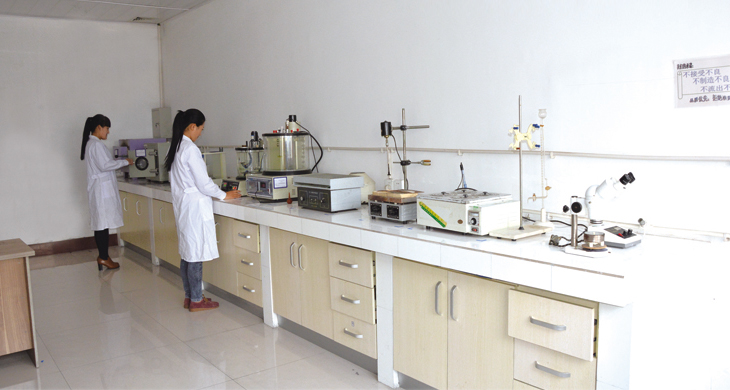
–Chemical Testing
Our chemical testing laboratory conducts chemical / material analysis of rubber and polymeric materials used for manufacturing automotive sealing products, industrial rubber seals, rubber extrusions, profiles, and molded rubber parts, etc. This testing laboratory offers a full range of chemical / material analysis services to evaluate rubber materials, and we perform tests utilizing a wide range of analytical methods, which enable us to accurately identify materials.
Typical Testing Equipment:
Number | Equipment Name | Usage |
#1 |
Tester for Oil Aniline Point Determination |
To determine the aniline & mixed aniline point of petroleum products and hydrocarbon solvents. |
#2 |
Viscometer for Kinematic Viscosity Determination |
Measure dynamic viscosity and derivation of kinematic viscosity of liquids. |
#3 |
Digital Analytical Balance (0.0001g Accuracy) |
Measure the weight and specific volume of rubber and other materials particularly of value in cellular sponge compounds. |
#4 |
Electro-thermal Constant-temperature Drying Oven |
To dry materials, samples as preparation
for next step testing |